Supplier Responsibility
By MacRumors Staff
Supplier Responsibility Articles
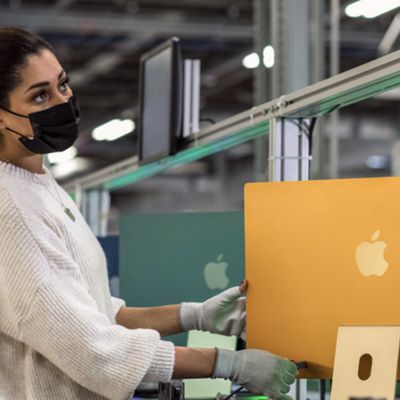
Apple Releases 2022 Supply Chain Progress Report, Launches $50 Million Skills Development Fund
Apple today released its 16th annual People and Environment in Our Supply Chain report. Previously known as the Supplier Responsibility report, the document details how Apple and its suppliers are supporting people across the company's supply chain, transitioning to clean energy, and investing in innovative technologies.
Apple also announced a new $50 million Supplier Employee Development...
Read Full Article 38 comments
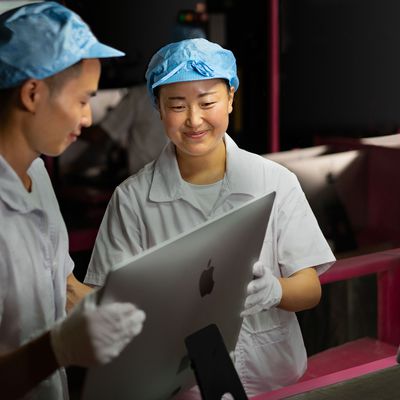
Apple Publishes 2021 Supplier Progress Report
Apple has published its annual supplier responsibility report, which outlines the progress it and its suppliers are making towards improving the rights of workers, furthering environmental protection goals, the response to the global health crisis, and more.
The report contains detailed information ranging from how Apple addresses reports of violations within its supply chain to how the...
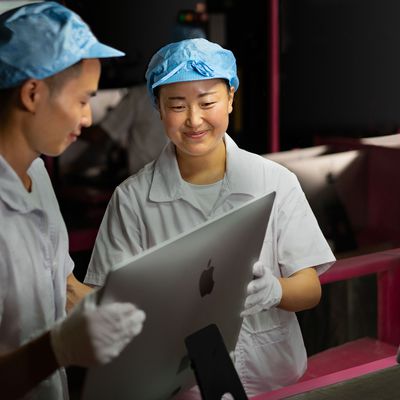
Apple Shares 2020 Supplier Responsibility Report Detailing COVID-19 Precautions
Apple today shared its 2020 Supplier Responsibility progress report [PDF], and as noted by TechCrunch, it includes a letter that details Apple's plans to increase safety and protection in its worldwide supply chain in the wake of the coronavirus outbreak.
Authored by Sabih Khan, Apple's senior vice president of operations, the letter details changes that Apple has made to protect its supply...
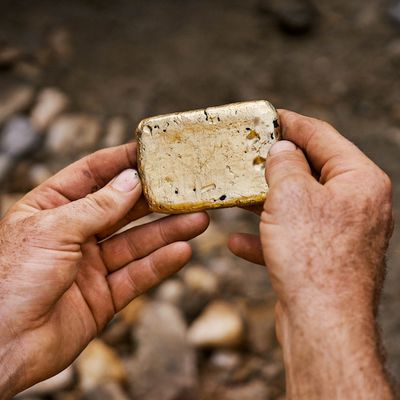
Apple Partners With RESOLVE in Effort to Source Gold From Miners Committed to Habitat Restoration
Apple today announced it has partnered with non-profit organization RESOLVE to seek out innovative ways to source gold responsibly.
The problem: gold mining operations in Alaska and the Yukon region have resulted in a reduction in the salmon population in the creeks and streams being mined. RESOLVE's solution: combine mining with habitat restoration to improve the streams so that salmon and...
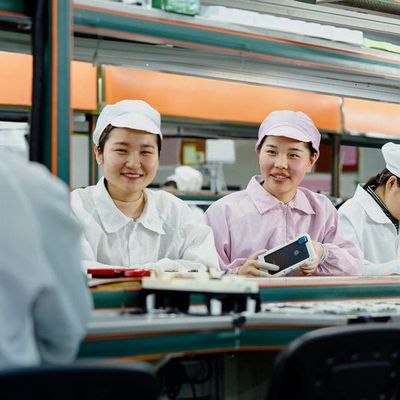
Apple Releases 2019 Supplier Responsibility Progress Report
Apple today released its 2019 Supplier Responsibility Report, offering a look into Code of Conduct violations in Apple's supply chain and details on progress made with programs promoting health, education awareness, and more.
Apple shares an updated Supplier Responsibility Report on an annual basis in an effort to be transparent about the worker conditions in supplier factories and the steps...
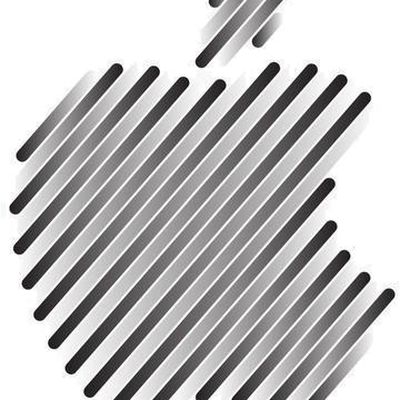
Apple Releases 2018 Conflict Minerals Report, Remains 'Deeply Committed' to Responsible Sourcing
Apple today filed its 2018 Conflict Minerals Report with the SEC as part of its commitment to supplier responsibility.
Apple said it remains "deeply committed" to upholding human rights across its global network of suppliers and "works to safeguard the well-being of people involved in its supply chain and to protect the places where materials are sourced."
Apple commits to use minerals in ...
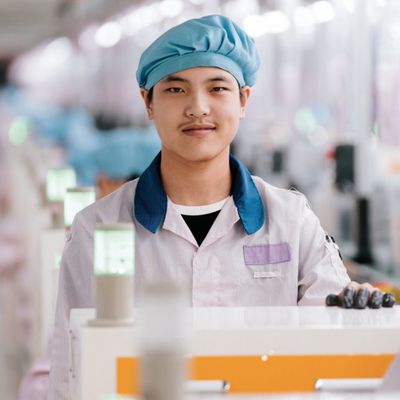
Apple Investigating Report of Forced Student Labor at Chinese Factory
Apple today said it is "urgently investigating" a report that claims Apple Watch manufacturer Quanta Computer has subjected teenage students to illegal work conditions at its factory in the Chinese city of Chongqing.
"We are urgently investigating the report that student interns added in September are working overtime and night shifts," Apple said, in a statement issued to CNN. "We have zero ...
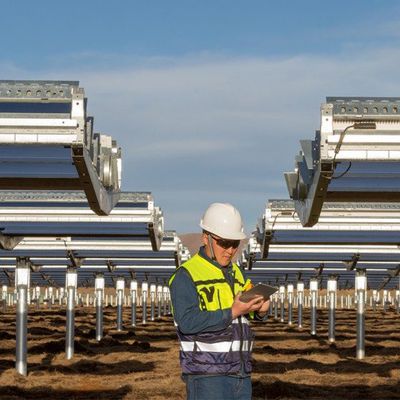
Apple Announces New $300 Million Clean Energy Fund in China
Apple today announced the launch of a $300 million investment fund in China which is designed to connect Apple's suppliers with renewable energy sources.
Apple, along with 10 initial suppliers, is investing $300 million into the China Clean Energy Fund over the course of the next four years. Apple says the fund will invest in and develop clean energy projects totaling more than 1 gigawatt of...
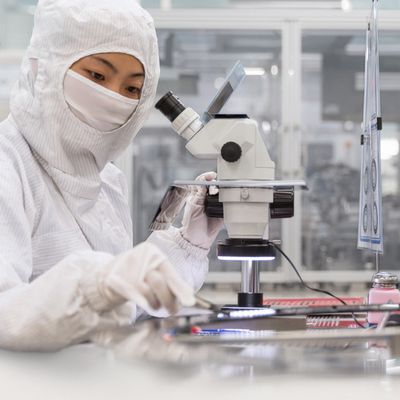
Apple Taking Action After Students Worked Overtime to Assemble iPhone X at Foxconn
Apple and its manufacturing partner Foxconn have confirmed instances of students working overtime to assemble the iPhone X, and both companies are now taking remedial action, as reported by the Financial Times.
A technician inspecting iPhone components at a factory
Apple conducted an audit and confirmed "instances of student interns working overtime at a supplier facility in China," according ...
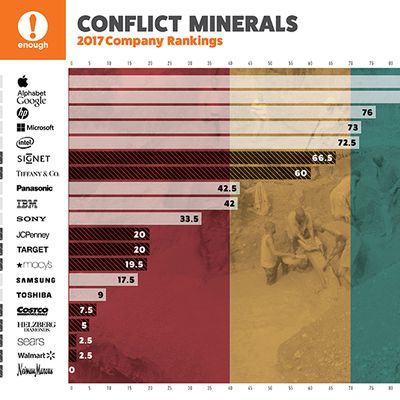
Apple Ranked as 'Clear Leader' in its Efforts to Source Conflict-Free Minerals From Supply Chain
Apple has been designated the "clear leader" in its methods of supporting a conflict-free minerals trade throughout its supply chain. The title was awarded to the company in a report published by the Enough Project, called the 2017 Conflict Minerals Company Rankings, in which Apple sits at the #1 spot. Rounding out the top 5 spots are Alphabet/Google at #2, HP at #3, Microsoft at #4, and Intel at ...
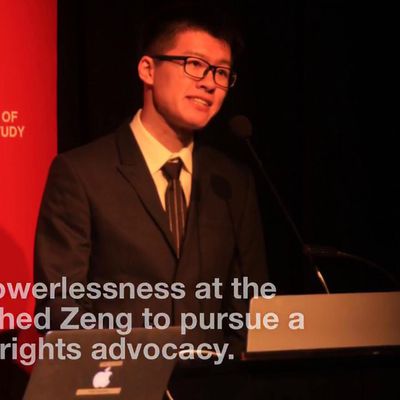
NYU Student Goes Undercover at Pegatron Factory, Offers Inside Look at iPhone Production
New York University graduate student Dejian Zeng spent last summer working in a Pegatron factory manufacturing the iPhone 6s and 7 as part of a summer project, where he got a first hand look at what factory life is like for a worker in China.
Zeng did a extensive, detailed interview with Business Insider, where he shared his experience and offered up an inside glimpse at how factories like...
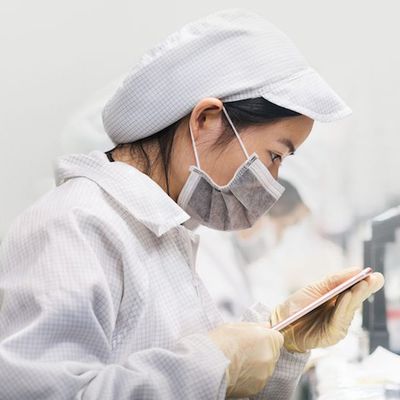
Apple's 2017 Supplier Responsibility Report Highlights Cobalt Supplier Audits, 98% Work Hour Compliance
Apple today released its 2017 Supplier Responsibility Progress Report, outlining progress that the company has made in its supply chain by highlighting its "highest ever" work hour compliance, advocating the success of Apple's Supplier Education Program, and celebrating more than 2.4 million workers who were trained on their rights last year. Apple releases such progress reports each year as a...
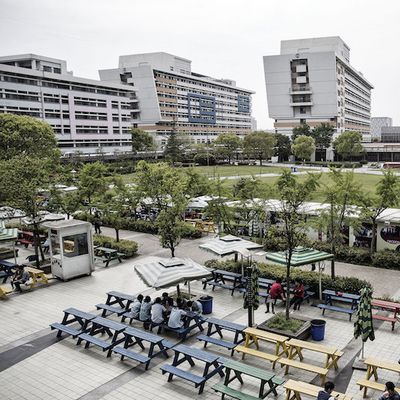
First Look Inside Pegatron's Secretive Shanghai iPhone Assembly Plant
Bloomberg has been granted an exclusive look inside a Chinese iPhone manufacturing plant where Apple claimed it has addressed cases of excessive overtime.
Pegatron Corp.'s sprawling facility on the outskirts of Shanghai covers an area equal to 90 football fields and employs some 50,000 people in the iPhone assembly process.
After accusations that employees were forced to work long,...
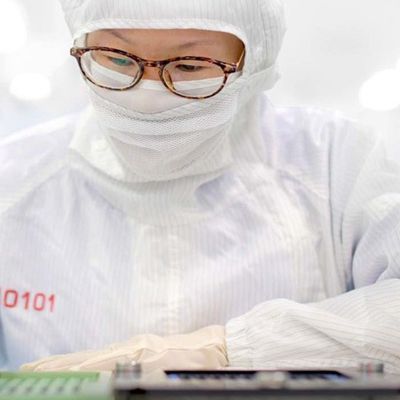
Apple Outlines Milestone on Eliminating Conflict Minerals in 2016 Supplier Responsibility Report
Apple today released its 2016 Supplier Responsibility Progress Report [PDF] and updated its accompanying Supplier Responsibility website to offer a look at its 2015 efforts to improve the lives of the workers that produce and assemble its products.
Apple's focus in 2015 was on cutting down on excessive work hours and addressing bonded and underage labor practices. Work-hour compliance on...

Apple Outlines New Ban on Bonded Labor at Supplier Factories in 2015 Progress Report
Apple on Wednesday released its 2015 Supplier Responsibility Progress Report [PDF] and updated its Supplier Responsibility website, giving new details on its efforts to improve the lives of the workers that assemble its products.
For its ninth annual progress report, Apple conducted 633 audits covering more than 1.6 million workers in 19 countries, and called an additional 30,000 workers to...

BBC Documentary Claims Apple Fails to Protect Chinese Factory Workers
Earlier this week, BBC One announced plans to air a documentary called Apple's Broken Promises, detailing the factory conditions of the overseas workers who are creating components and assembling the company's iPhones.
Apple's Broken Promises is set to air tonight, but ahead of the documentary's launch, BBC News has published a story outlining what they discovered when they visited Pegatron...
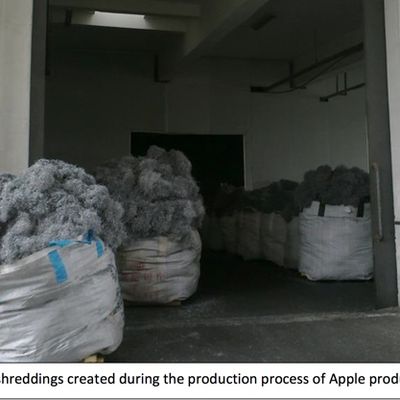
Apple Supplier Catcher Accused of Endangering and Exploiting Factory Workers
One of Apple's suppliers is once again being accused of labor violations, with both Green America and China Labor Watch claiming a Catcher factory in Suqian, China has endangered the health and safety of its workers. Catcher is responsible for producing casings for many of Apple's products, including its MacBooks and iPads.
According to the report [PDF], Catcher has failed to provide adequate...
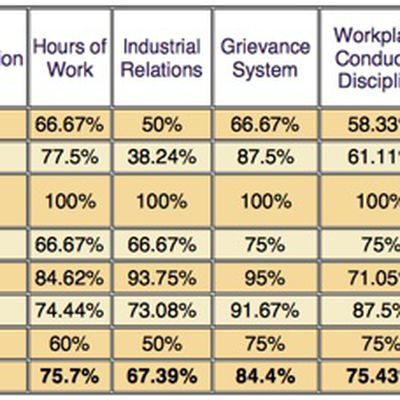
Apple Working to Remedy Labor Violations Found at Quanta Factories
The Fair Labor Association (FLA) today published a new report examining two factories operated by Apple-supplier Quanta Computer, finding several code violations related to working hours, recruitment policies, compensation, health and safety, and more in August of 2013 [PDF] (via TechCrunch).
Factories examined included a Quanta facility in Shanghai and one in Changshu. Quanta is a long-time...
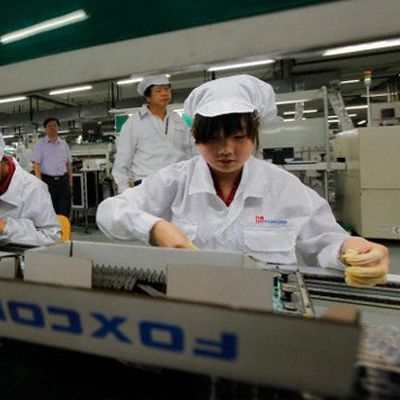
Apple Among Highest-Ranking Brands in Latest Workers' Rights Report
International aid organization Baptist World Aid Australia released its Electronics Industry Trends report that examines working conditions for employees throughout the technology supply and manufacturing chain (via ZDNet). Apple was one of the highest-ranking brands in the report, which includes suppliers in all facets of the supply chain starting with mineral extraction and extending to the end ...
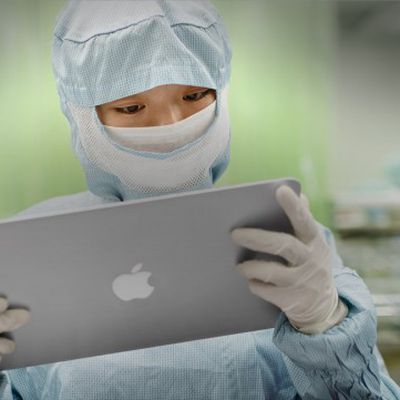
Apple Confirms Suppliers Do Not Use Unethically Sourced Tantalum
Apple today published its 2014 Supplier Responsibility Report, releasing the results of its supplier audit program for 2013 and confirming that its partners only use ethically sourced tantalum, which is a primary metal used in electronic components that can be also be mined from war-torn regions in Africa.
In January 2014, we confirmed that all active, identified tantalum smelters in...